La revisión de equipos industriales suele estar enmarcada en una planificación que contempla acciones programadas y un protocolo de respuesta ante contingencias. Conocé de qué se trata.
Toda industria requiere que sus instalaciones y equipos se mantengan en óptimas condiciones: no solo para garantizar la producción y evitar paros de actividad costosos, sino también para procurar la seguridad y salud de sus trabajadores.
Los equipos industriales en particular requieren una atención especial, ya que con frecuencia funcionan durante largas horas o días sin detenerse. Por eso, cualquier máquina industrial ⏤más allá de su función⏤ necesita revisiones periódicas y sistemáticas si queremos que funcione al máximo de su capacidad, y logre cumplir con su ciclo de vida.
Mantenimiento preventivo, correctivo y predictivo
La revisión periódica de los equipos industriales suele estar enmarcada en una planificación que contempla acciones programadas y un protocolo de respuesta ante contingencias. Este plan se plasma en un documento donde figuran los procedimientos, recursos y las intervenciones de mantenimiento, teniendo también en cuenta:
- Las recomendaciones del fabricante de cada máquina.
- Las normativas y reglamentos de aplicación de cada caso.
- Y las observaciones de los trabajadores u operarios.
En este plan de mantenimiento pueden contemplarse, a grandes rasgos, tres tipos de tareas de mantenimiento: las preventivas, las correctivas y las predictivas.
El mantenimiento preventivo tiene como principal objetivo reducir riesgos y, a la vez, garantizar que las máquinas funcionen en forma eficiente. Las tareas de mantenimiento preventivo evitan fallos o desperfectos en los equipos a partir de una revisión sistemática e integral de sus componentes clave, incluyendo aspectos de seguridad, calibración, mecánica y electricidad (entre otros). Al tratarse de una revisión sistemática, este tipo de mantenimiento suele llevarse a cabo siguiendo parámetros y protocolos específicos establecidos de antemano en la planificación.
Como sugiere su nombre, el mantenimiento correctivo es aquel que atiende un problema o avería una vez que se ha producido. En este caso, el tiempo de reparación y la consiguiente inactividad de los procesos productivos puede representar un alto costo para las empresas, por lo que, idealmente, las tareas de mantenimiento correctivo deben realizarse lo antes posible y de la mejor manera, para minimizar el impacto en la producción. Con frecuencia, las tareas de reparación incluyen el análisis, diagnóstico, ingeniería, fabricación y reemplazo de piezas en los equipos.
Finalmente, el mantenimiento predictivo se basa en el registro e interpretación de datos estadísticos y variables de actividad de los equipos para evaluar su estado y detectar oportunidades de mejora. El seguimiento pormenorizado del funcionamiento permite detectar la presencia de valores anómalos, y alertar a los responsables para que procedan a realizar una revisión o reemplazo del componente antes de que ocurra un fallo. De esta manera, el mantenimiento predictivo logra optimizar la fiabilidad y disponibilidad de los equipos a un costo mínimo.
Adicionalmente, algunos expertos consideran también un cuarto tipo de mantenimiento, llamado de “cero horas”, en el que se realizan tareas de reemplazo o reparación de elementos desgastados en forma programada. Esta forma de mantenimiento es muy importante y tiene notables efectos en la vida útil de los equipos, pero es habitual que sea contemplada como una tarea más dentro de los programas de mantenimiento preventivo.
La reparación de piezas y el diseño de nuevos repuestos
La vida útil de la maquinaria industrial es uno de los factores clave en los presupuestos y la productividad de las empresas. Su control efectivo redunda en la eficiencia de los procesos productivos, lo cual lleva a ahorrar mucho tiempo y dinero.
Sin embargo, ya sea que esté contemplado o no en el plan de mantenimiento, siempre existe la necesidad de reparar, reemplazar u optimizar piezas para prolongar el ciclo de vida de la maquinaria. Y el costo derivado de estas reparaciones ⏤incluyendo materiales, asistencia técnica especializada y servicios subcontratados⏤ puede ser alto cuando no se cuenta con un socio estratégico que aporte soluciones de calidad.
En ese sentido, una solución realmente integral se caracteriza no solo por entregar en tiempo y forma una pieza bien diseñada, sino también por escuchar al cliente, entender la verdadera dimensión de sus necesidades, y acompañarlo para que su producción mantenga siempre los mejores estándares de calidad del mercado. Eso es lo que hacemos en Metalúrgica Daniele.
Buscando establecer relaciones comerciales de largo plazo en las que predomine un espíritu “ganar-ganar”, nos enfocamos en erradicar los problemas de raíz, generando una excelente satisfacción en nuestros clientes y mostrándonos siempre dispuestos a afrontar nuevos desafíos.
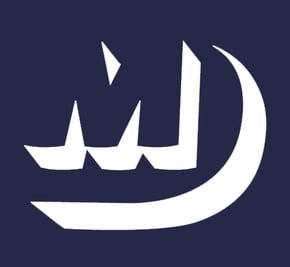