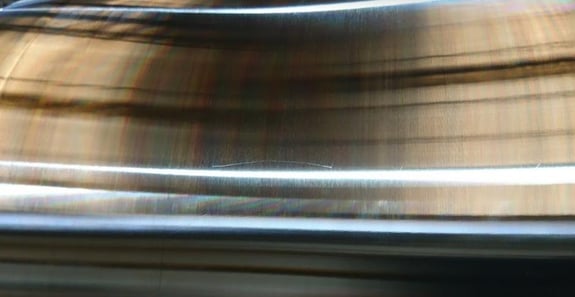
A solution for Trivium Packaging Argentina
Get up close and personal with how we work. Today we share the case of Trivium Packaging S.A., a multinational company dedicated to the manufacturing of a wide variety of metal containers.
Trivium Packaging S.A. is a multinational company dedicated to the manufacturing of a wide variety of metal containers, including screw bottles, aerosols, beverage containers, food cans and other containers created from steel, tinplate and aluminum. Founded in 2019, the company has more than sixty offices around the world, distributed in 20 countries. In Argentina, it has branches in Buenos Aires and Chubut, where yew trees are produced for the manufacture of aluminum containers through impact extrusion.
In April 2019, we received a visit from a representative of Trivium Packaging, who approached us to ask us about the best way to solve a series of problems they were having at their Puerto Madryn plant with the rolling mill. Specifically, the yew trees they produced often had a thickness outside of tolerance for the market in which the company sought to compete. Besides:
The lamination process was not 100% controlled.
SKF and other alternative brand bearings had a very short useful life, 15 to 20 days.
They needed to start rolling harder aluminum alloys.
Our solution
At Daniele, we proposed to carry out a standardization and improvement of the lamination roller assemblies, so that the production process would always remain within the established parameters and, at the same time, the useful life of the parts would be extended.
He worked with the client to define a new coding system to begin recording the dimensions of the elements in this new stage of repairs. The best method was also sought to achieve the roughness required by the client on the rolling roll, define tolerances and adjustments, and survey/sketch when necessary.
Roller trunnion being machined for later casing.
Initially, the client did not have a large amount of supplies and parts for the proper maintenance and tuning of the rolling mill (such as bearings, grease, seals, rollers, and pockets). Therefore, resources had to be optimized based on the existence of these elements, with the aggravating factor that the assemblies that were on the production line had an imprecise and unstable duration, which put the existing inventory in check.
Precise machining, detailed inspection during disassembly, methodical assembly and conscientious recording were proposed to control and detect anomalies in old elements, thus avoiding future problems in the rolling mill. Details of assembly and disassembly, and specific maintenance tips were also shared, obtaining a round trip of information beneficial to everyone.
Leonardo Piccardo, Head of Maintenance at Trivium Packaging in Argentina, shared his experience with us:
“Working with Daniele's team was very rewarding. They perfectly understood the problem and the urgency with which we needed a solution, and they helped us optimize our lamination process in record time. We are very happy with the results”.